Building the Impossible: A 20,000 SQFT Medical Device Manufacturing Clean Room in Record Time
During the onset of the pandemic, Thermo Fisher experienced a significant increase in the demand for plastics for laboratory product essentials. To meet this skyrocketing demand, they required a large, high-quality cleanroom built to meet Good Manufacturing Practices (GMP) standards – and fast.
Unique Requirements: Finding a clean room manufacturer capable of handling this project is proving difficult. Thermo Fisher needs a partner who could deliver on several key aspects:
- Scale: The medical device manufacturing clean room has to be extensive to accommodate significant production volume.
- Short Timeline: Time was of the essence as the clean room needed to be operational urgently. Traditional construction timelines wouldn’t suffice.
- Quality: Maintaining superior clean room conditions was paramount for product sterility and compliance with GMP regulations.
- Design Specificity: The clean room design needed to incorporate specific criteria unique to Thermo Fisher’s operations.
MECART answered the call and did what no other competitor could.
MECART was the only vendor at the time who could meet our timeline, no other competitor could come close to meeting those timelines
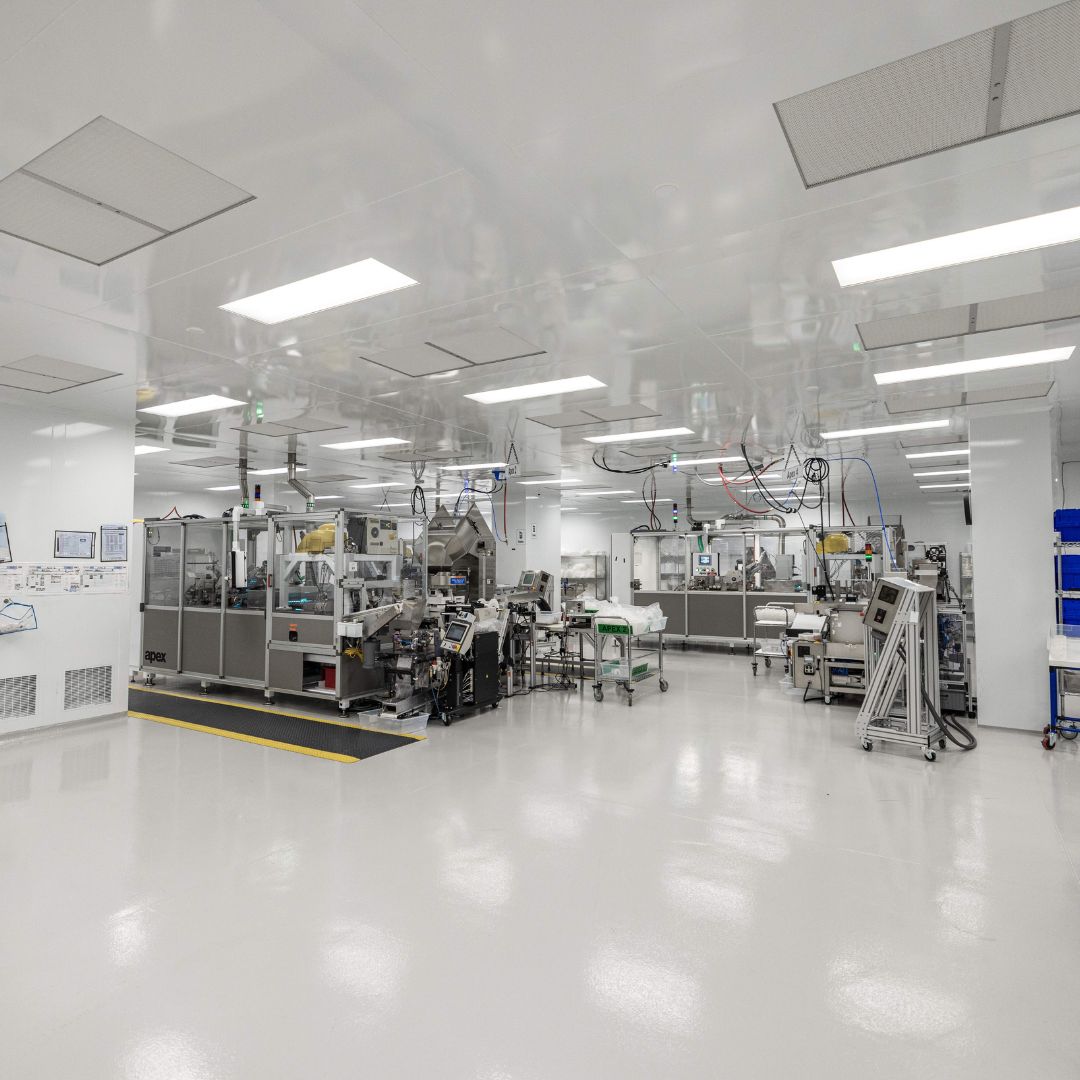
Fast Turnaround: 20,000 SQFT Medical Device Clean Room Delivered Under 4 Months
‘’MECART was the only vendor at the time who could meet our timeline, no other competitor could come close to meeting those timelines.’’
Doug Anderson, Facility Engineer at Thermo Fisher Scientific
- Traditional cleanroom manufacturers struggled to meet Thermo Fisher Scientific’s demanding timeline.
- MECART, with its streamlined processes and high-volume manufacturing, committed to delivering the cleanroom in under 4 months.
- Thermo Fisher was impressed with MECART’s adaptability, creativity and ingenuity to make it happen for them.
After reaching out to multiple cleanroom manufacturers, they were met with a consistent response from each one when they outlined the project’s scope: it would be impossible to complete such a large project within the given timeframe.
At MECART, we understand the urgency some projects demand. We take a different approach. By streamlining our processes, leveraging our in-house expertise, and capitalizing on an agile supply chain – all backed by high-volume manufacturing capacity – we were confident we could deliver this large-scale cleanroom despite the short deadline.
Thermo Fisher inked the deal in August and by December, MECART delivered the 20,000 sqft medical device manufacturing clean room – fully operational in under 4 months.
Our success on a task deemed improbable by Thermo Fisher left a strong impression.
”We chose MECART as a supplier and manufacturer for our cleanroom because of the quality of their design, and the efficient timeline they can complete the project in. We built a large 20,000 square foot cleanroom here in under four months, which is extraordinary.”
Don’t Let Tight Deadlines Stall Your Medical Device Production
The product line that MECART proposed to us was of quality greater than anything else we have in our facility
Impress Leadership & Raise Standards with MECART Medical Device Manufacturing Clean Rooms
‘’The product line that MECART proposed to us was of quality greater than anything else we have in our facility.’’
Doug Anderson, Facility Engineer at Thermo Fisher Scientific
Thermo Fisher, a powerhouse in the life sciences and medical equipment industry, is no stranger to cleanroom environments. Their Rochester facility alone boasts 10 daily operational cleanrooms.
Yet, MECART demonstrably raised the bar for Thermo Fisher. They found MECART’s clean room to be a significant upgrade compared to their existing medical device manufacturing clean rooms.
Thermo Fisher praises MECART’s cleanroom for its superior design, construction, and engineering. These features create a best-in-class cleanroom environment, ensuring efficient and reliable injection molding operations.
- cGMP compliance: Ensures adherence to strict manufacturing regulations, giving you peace of mind.
- Flush-finish design: Eliminates crevices where dust and particles can accumulate, reducing the risk of contamination
- Harsh-chemical resistant panels: Enables easy cleaning and disinfection, maintaining a sterile environment for your injection molding processes
‘’This is the first clean room here, the MECART clean room, that’s truly a clean room. The one that we’ve built is efficient. It’s airtight. It’s a true dual-wall construction. It’s a structure, not just a clean room, and nothing else we have here comes close to that MECART clean room. And it really impressed our leadership with its quality.’’
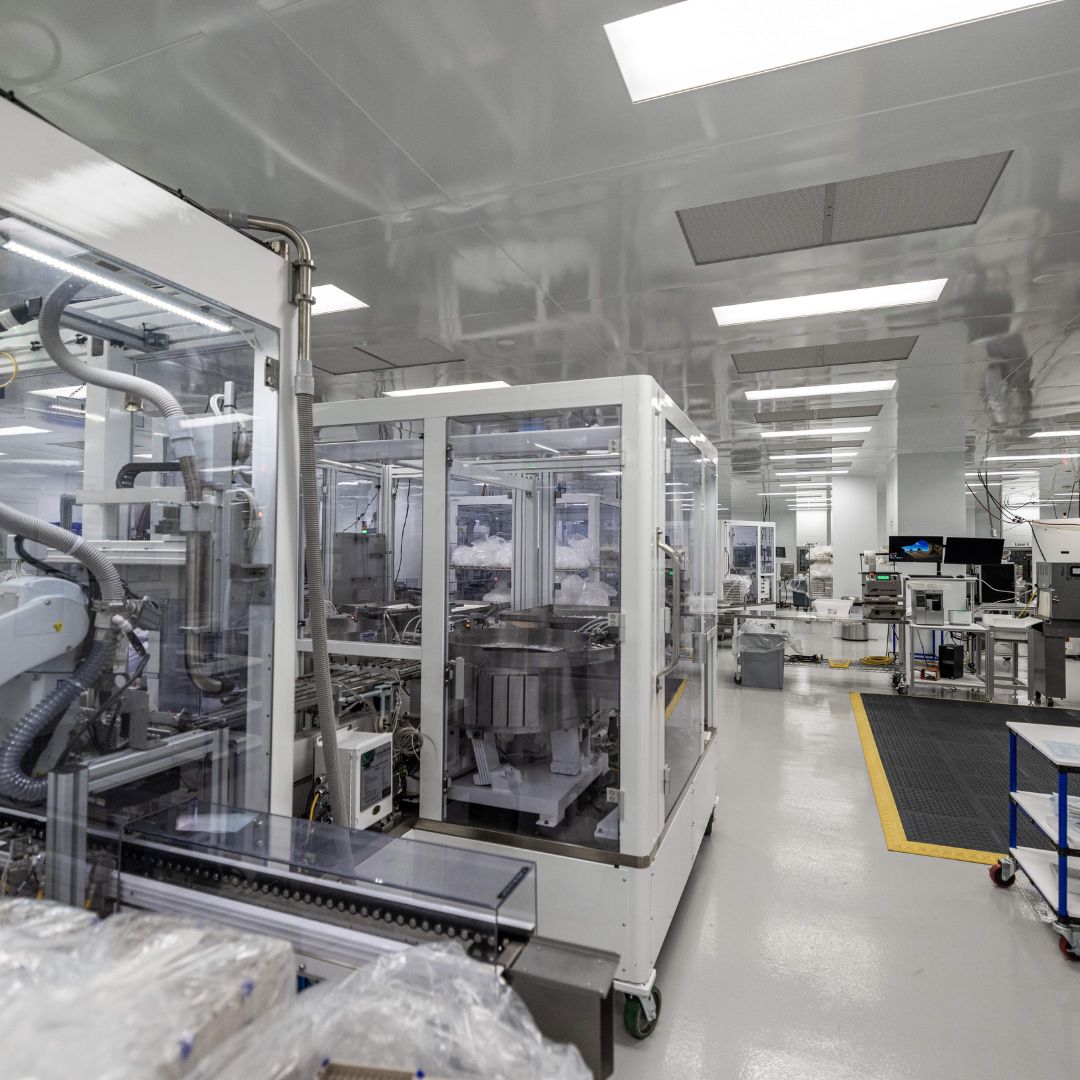
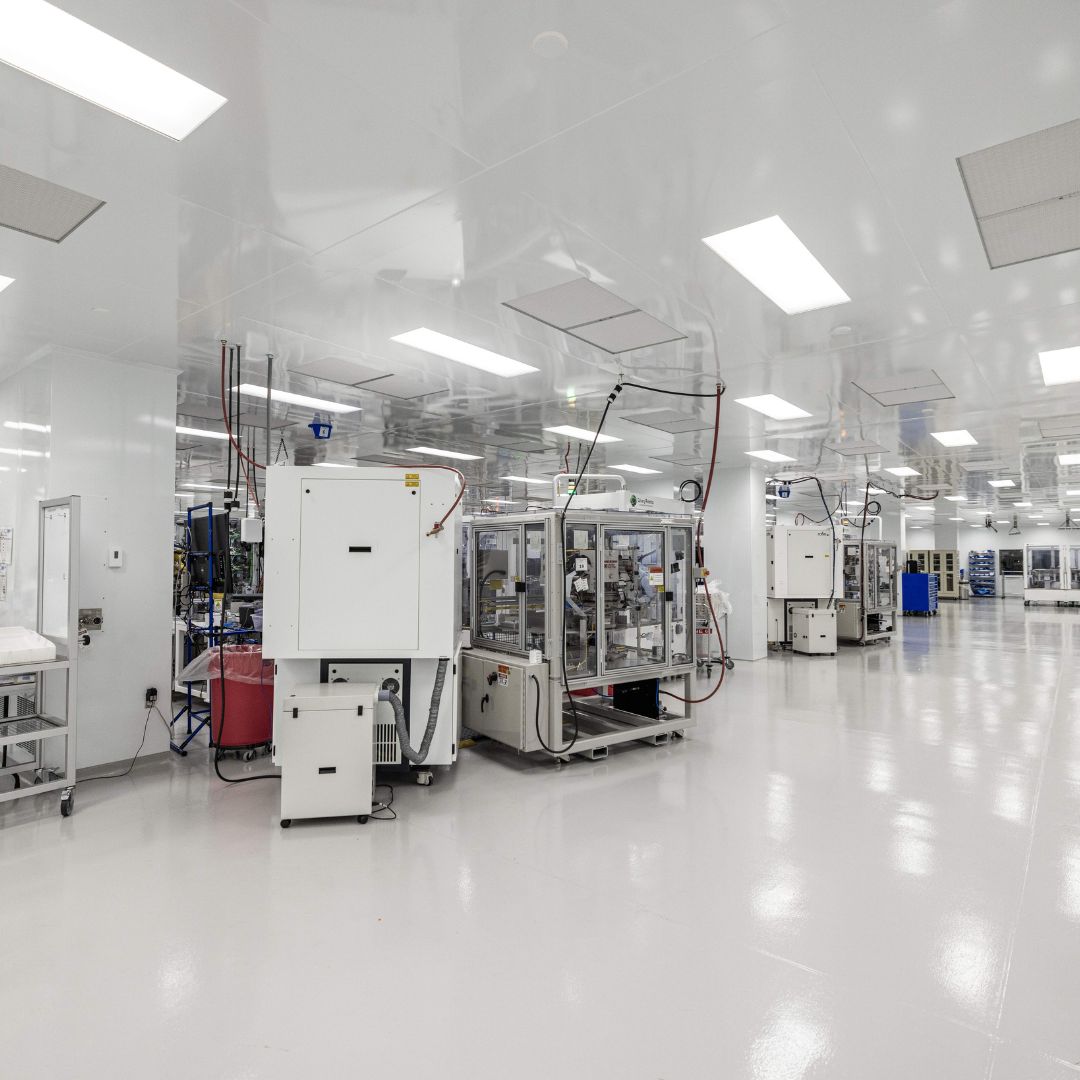
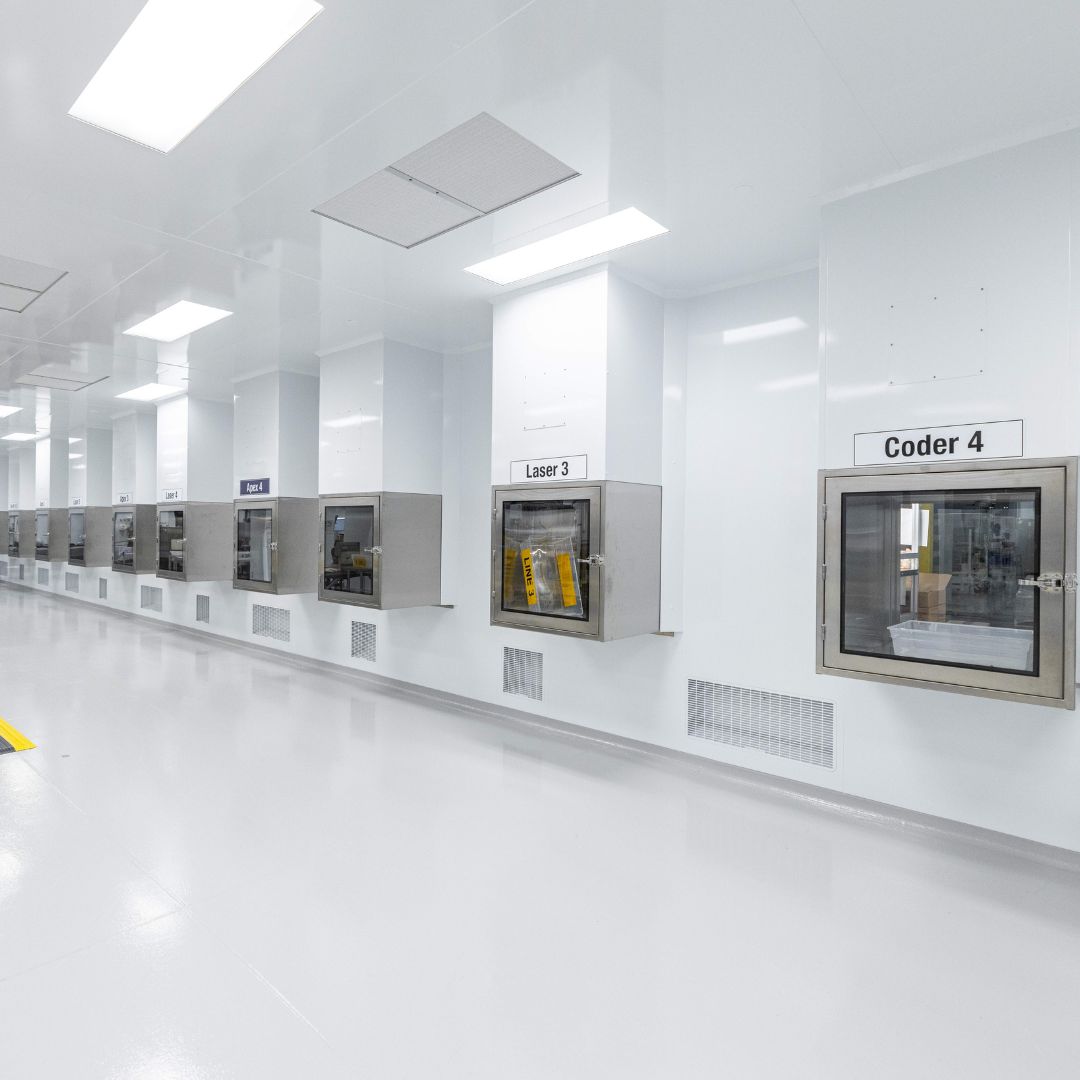
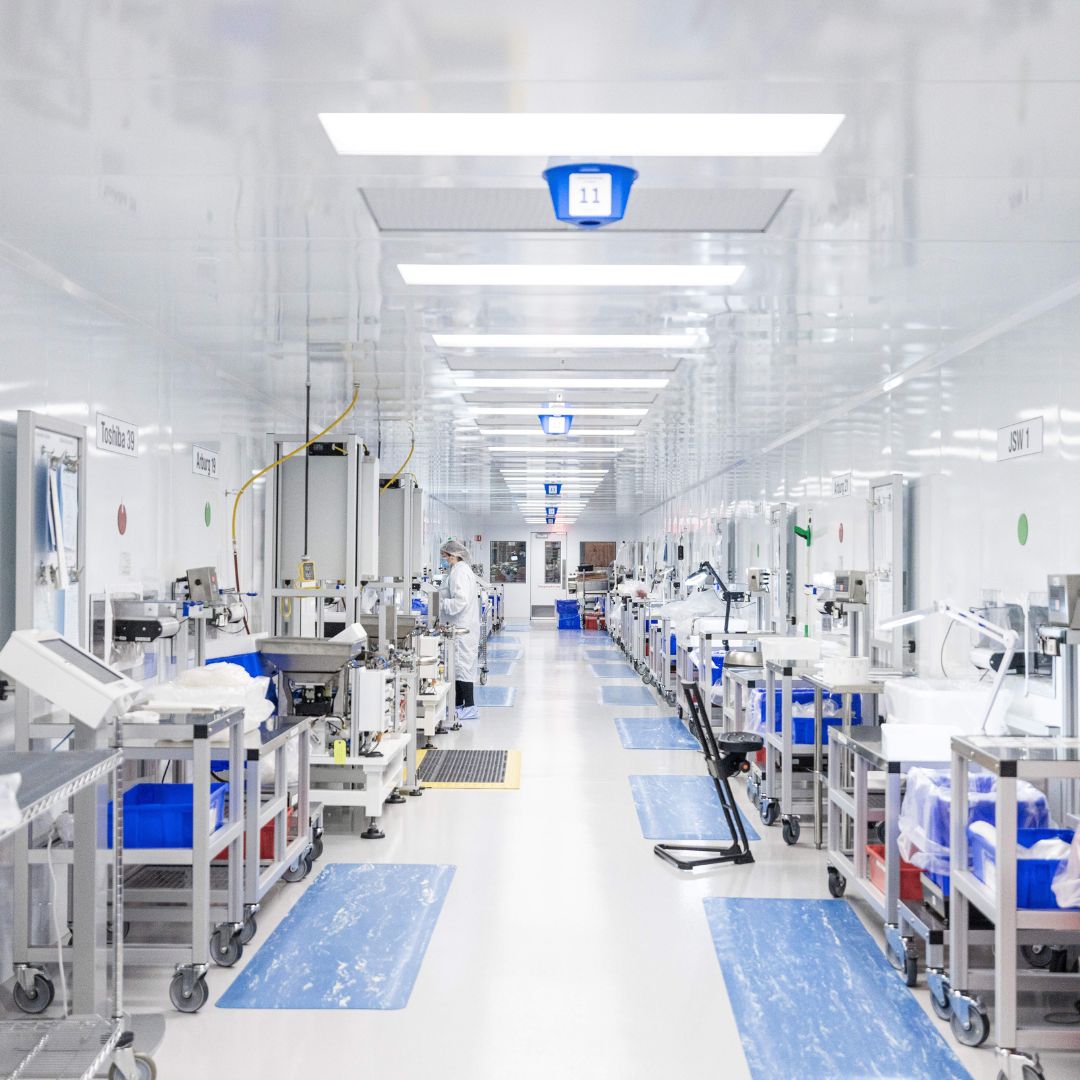
Beyond Standard Solutions: Customizing the Ideal Medical Device Manufacturing Clean Room
MECART recognizes that every business has specific clean room requirements. Unlike manufacturers offering standardized solutions, we specialize in fully customizable clean rooms to guarantee a perfect fit for your unique needs.
Thermo Fisher tasked MECART with customizing their medical device manufacturing clean room for both functionality and aesthetics.
Their priorities included removable wall panels for easy equipment replacement, 20 pass-through windows for product flow, and a custom skirt to hide HVAC ducts.
Customization for Large Equipment
- Removable Wall Panels: Due to the large size (9 feet) of some equipment, MECART designed and fabricated 10×10 feet removable wall panels. These panels could be unbolted using a forklift to allow for bringing in large equipment that wouldn’t fit through standard clean room doors.
Product Transfer Integration
- Custom Conveyor Windows: Since the T-shaped clean room had ten molding machines on each side feeding into it, MECART custom-fabricated and installed 20 conveyor windows. These windows enabled efficient product transfer from the factory floor directly into the clean room.
Efficiency in Design
- Custom Skirt: To provide a clean and finished look, MECART designed and installed a custom skirt around the top of the clean room. This concealed all the exposed ductwork and utilities in the interstitial space.